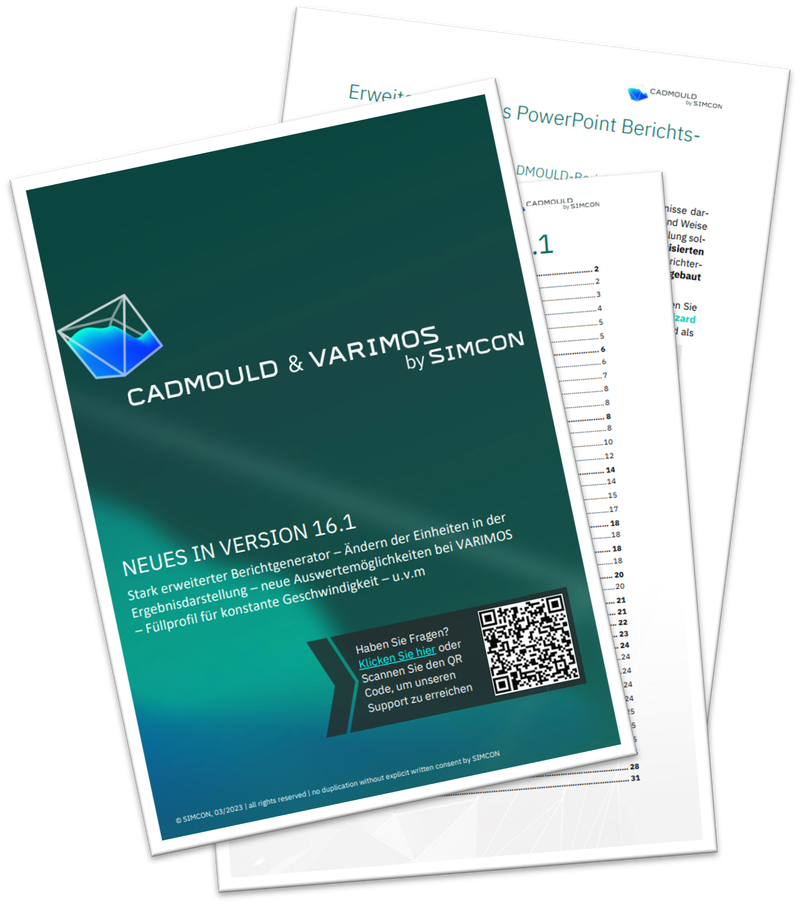
1 minute lesen
Tear down this wall: ARBURG & SIMCON Verbinden Simulation und Maschine
Die papierlose Übertragung von Parametern von der Simulation zur Spritzgießmaschine ist entscheidend, wenn Spritzgießer bessere Ergebnisse erzielen wollen.
Read More