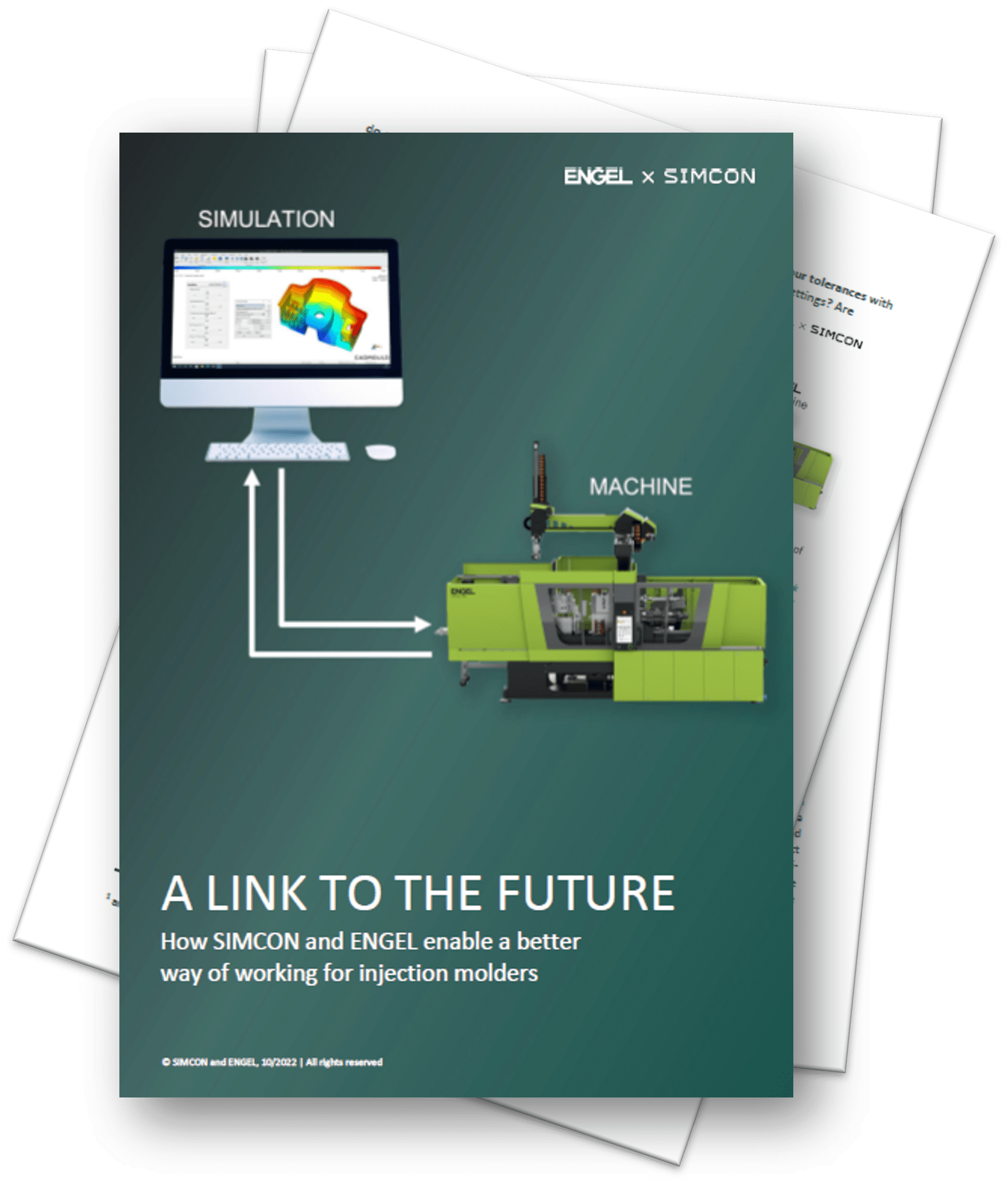
1 min read
Link to the future: How ENGEL & SIMCON enable a better way of working
Bi-directional communication between the simulation and the machine makes it easier for engineering and the shop floor to collaborate effectively.
Read More1 min read
Bi-directional communication between the simulation and the machine makes it easier for engineering and the shop floor to collaborate effectively.
Read More1 min read
Paperless parameter transfer from simulation to the injection molding machine is crucial, if injection molders want better results.
1 min read
Fast series production with significantly reduced warpage. This was the result of PLASTON and GOLLMER Formen working together to refine the mold...
3 min read
Kadkraft Systems, with over 3 decades of experience in distributing CAD/CAM, gearbox, and manufacturing simulation solutions in India, is now joining...
2 min read
Find out what the advantages and disadvantages of plastic injection molding simulation are. Our opinion: if the prerequisites are right, it only...
1 min read
You are looking for a new plastic injection molding simulation software and not quite sure where or how to start your search and what exactly is...
2 min read
2020 has been a challenging environment for many companies, on many fronts. Due to the pandemic, the macroeconomic climate has been challenging....
3 min read
Koorean CAD/CAM specialist INCOS INC is now distributing SIMCON’s plastic injection molding simulation and optimization software CADMOULD and VARIMOS.
2 min read
1. Use The Right Material And Not Too Much Of It! Which material you choose has a significant impact on your costs. The material you initially select...
3 min read
Shanghai, People’s Republic of China, March 18, 2021 Simulation and optimization solutions now available at ZIMMY, China Digital engineering...